Stirling Energy Systems' 25 kW solar dish harnesses the power of the sun to make zero emissions energy. Stirling Energy Systems (SES) is a U.S. Phoenix, Arizona based company and recently (April 17, 2008) they announced that the company NTR plc of the United Kingdom had invested $100 million in them to take a controlling stake. On February 12, 2008 Stirling Energy Systems achieved a record 31.25% net efficiency in the conversion of solar energy to electricity, beating the earlier 29.4% efficiency of a Stirling Solar Dish set by Sandia National Laboratories in 1984.
Stirling Energy Systems' Solar Dish Engine has the commercial brand name of 'SunCatcher' and was developed in 1984 by McDonnell Douglas Corporation and Kockums of Malmo, Sweden. With the acquisition of McDonnell Douglas by Boeing, Boeing assumed the rights to the technology. In 1996 Stirling Energy Systems acquired the patent rights and a license to build the Kockums 4-95 Stirling Engine from Boeing. Boeing and SES continued to work jointly on the development of the Stirling Engine in conjunction with the U.S. Department Of Energy (DOE) as Phase I and II development trials between 1999 and 2001.
The Dish Stirling Engine is comprised of the solar concentrator and the power conversion unit (PCU). The PCU is a four cylinder hydrogen gas sealed arrangement and the cylinder assemblies are comprised of pistons and connecting rods along with coolers, regenerators, and heater heads. The entire PCU is held on the receiver arm of the dish. The heat transfer from solar rays to the heater head causes the hydrogen gas to expand in the piston and be exchanged between cylinder arrangements giving a maximum 1800 rpm speed and an output of 480 volts at 60Hz - all of this powered by the Sun with zero emissions to the environment.
SES's two most recent awarded contracts are: one from Southern California Edison (500 MW - signed 2005) for first phase completion Jan 2009, and one from San Diego Gas & Electric (300 MW - signed 2005). A 500 MW solar facility can power approximately a quarter million homes. Both of these contracts have expansion phase 2 clauses that could grow the total combined order by another 950MW or 1750 MW in total and a production of 70,000 SES Dish Engines. SES will build and operate the two solar energy power projects and provide electricity to the utilities.
The SES consortium of shareholders currently focus on build-operate high volume Solar Dish energy farms whose electricity is sold to major power companies. It is definitely a company to watch if they decide to release an Initial Public Offering (IPO) for capital infusion and also start to sell units individually in the commercial marketplace. The NTR plc investment should give Stirling Energy Systems the required capital to comercialise the SunCatcher Solar Dish technology and lower it's per unit manufacturing costs. The SES Solar Dish has applicability to all high solar intensity regions for the generation of zero emissions energy.
Born at Cloag Farm near Methven, Perthshire, Stirling was the third of eight children. From 1805 to 1808, he attended Edinburgh University, studying Latin, Greek, Logic, Mathematics and Law. In November 1809 he studied Divinity at Glasgow University and completed five sessions.
In 1814, he continued his studies of Divinity at Edinburgh University and in 1815, the Presbytery of Dunbarton confirmed that Robert Stirling was competent to preach the Gospel. In March 1816 a license was issued to this effect. He was presented by The Commisioners of the Duke of Portland to the Presbytery of Irvine, and after examination was ordained Minister of the Second Charge of Laigh Kirk, Kilmarnock on the 19th September, 1816.
At an early age, Robert had been introduced to engineering by his father (as was his younger brother James who became a civil engineer), Patrick Stirling, who in turn had helped his his own father, Michael, in maintaining threshing machines. Machinery and methods of mechanical power was an interest that permeated the Stirling family.
For some years before moving to Kilmarnock, Robert Stirling had been working on his engine (to be known as The Heat Economiser) and continued work on his design in his new position after arriving in Kilmarnock. On 27th September, 1816, Robert Stirling applied for a patent for his heat engine. The patent was registered on the 20th January 1817.
Stirling married Jean Rankin on 10th July 1819. She was the daughter of William Rankin, a wine merchant in Kilmarnock, and Jean McKay. They had seven children.
Kilmarnock was also to be the place where Robert Strirling became involved with Thomas Morton. Morton was the son of a brick manufacturer, and had served an apprenticeship as a turner and wheelwright. Morton had set up his own business and was a keen innovator and embraced the ideas of the day. His engineering success included improving carpet loom techniques. Both Morton and Stirling were keen astronomers and in 1818 Morton constructed an observatory at his premises, Morton Place.
Robert Stirling was able to agree with Thomas Morton to acquire workspace at Morton Place where he could continue his experiments. Stirling was to use these premises for some 20 years. It was not just air engines that Stirling contributed to, he was also to contribute to the field of lenses and optics and this was probably due to Morton's interests and collaboration. No doubt his brothers and particularly James, encouraged Stirling with exchanges of ideas and practical contributions to his research.
From this brief biography, it is clear to see that Robert Stirling was well educated in the classics, the mathematics of the day, and he had a particular affinity with engineering ideas and principles. His work in the Church underpinned his daily life, in a family that shared his passions and with a colleague in Thomas Morton, Stirling was able to flourish in his lifetime. Stirling also had the reputation as a wonderful speaker and was well loved by his parishioners.
His children's achievements are testimony to the hereditary traits, influences and values of the family. The children of Robert and Jean Stirling were;
Patrick Stirling, born 29th June 1820, Railway Locomotive Engineer; Jane Stirling, born 25th September 1821; William Stirling born 14th November 1822, Civil Engineer and Railway Engineer in South America; Robert Stirling, born 16th December 1824, Railway Engineer in Peru; David Stirling, born 12th October 1828, Minister of Craigie, Ayrshire; James Stirling, born 2nd October 1835, Railway Engineer; Agnes Stirling, born 22 Jul 1838, talented artist, no popular reknown.
Stirling died in Galston, East Ayrshire in 1878. He left us with the Stirling engine as a mechanical engineering concept that can still be explored today. Perhaps the full potential of Stirling engines is still to be realised. The elegant, seemingly simple mechanics and by turn theoretical complexity still challenges our intellect today.
A Gamma type Stirling engine uses a displacer like a Beta Stirling but the power piston is mounted in a separate cylinder alongside the displacer piston cylinder. They are connected to the same flywheel. The gas in the two cylinders can flow freely between them and remains a single body. During the expansion process some of the expansion must take place in the compression space leading to a reduction of specific power.The gamma engine is mechanically simpler and often used in multi-cylinder Stirling engines. This configuration produces a lower compression ratio.
A Beta type Stirling engine has a single power piston and a displacer within the same cylinder and on the same shaft. The displacer piston is a loose fit and and is used only to move the working gas from the hot heat exchanger to the cold heat exchanger.
When the working gas is pushed to the hot end of the cylinder it expands and pushes the power piston. When it is pushed to the cold end of the cylinder it contracts and the momentum of the machine, pushes the power piston the other way to compress the gas. The beta type avoids the technical problems of hot moving seals (as in the alpha type).
1. Power piston (dark grey) has compressed the gas, the displacer piston (light grey) has moved so that most of the gas is adjacent to the hot heat exchanger.
2. The heated gas increases in pressure and pushes the power piston to the farthest limit of the power stroke.
3. The displacer piston now moves, shunting the gas to the cold end of the cylinder.
4. The cooled gas is now compressed by the flywheel momentum. This takes less energy, since its pressure drops when it is cooled.
An Alpha type Stirling engine contains two power pistons in separate cylinders. One cylinder is hot and one cold. The hot piston is situated after the higher temperature heat exchanger and the cold piston is situated after the low temperature heat exchanger. (In the diagram below, in the pipe connecting the two cylinders, internal heat exchangers are not shown in the compression and expansion spaces). A regenerator would be placed in the pipe connecting the two cylinders. The crankshaft has also been omitted.
This engine configuration results in a high power-to-volume ratio but the high temperature of the hot piston can create technical problems as the seals need to withstand high temperatures. To get over this problem a system is incorporated that carries a large insulating head to move the seals away from the hot zone at the expense of some additional dead space.
1. Most of the working gas is in contact with the hot cylinder walls, it has been heated and expansion has pushed the hot piston to the bottom of its travel in the cylinder. The expansion continues in the cold cylinder, which is 90° behind the hot piston in its cycle, extracting more work from the hot gas.
2. The gas is now at its maximum volume. The hot cylinder piston begins to move most of the gas into the cold cylinder, where it cools and the pressure drops.
3. Almost all the gas is now in the cold cylinder and cooling continues. The cold piston, powered by flywheel momentum (or other piston pairs on the same shaft) compresses the remaining part of the gas.
4. The gas reaches its minimum volume, and it will now expand in the hot cylinder where it will be heated once more, driving the hot piston in its power stroke.
A Stirling engine is a heat engine operating by cyclic compression and expansion of air or other gas, the working fluid, at different temperature levels such that there is a net conversion of heat energy to mechanical work. Or more specifically, a closed-cycle regenerative heat engine with a permanently gaseous working fluid, where closed-cycle is defined as a thermodynamic system in which the working fluid is permanently contained within the system, and regenerative describes the use of a specific type of internal heat exchanger and thermal store, known as the regenerator. It is the inclusion of a regenerator that differentiates the Stirling engine from other closed cycle hot air engines.
Originally conceived in 1816 as an industrial prime mover to rival the steam engine, its practical use was largely confined to low-power domestic applications for over a century.
The Stirling engine is noted for its high efficiency compared to steam engines,[4] quiet operation, and the ease with which it can use almost any heat source. This compatibility with alternative and renewable energy sources has become increasingly significant as the price of conventional fuels rises, and also in light of concerns such as peak oil and climate change. This engine is currently exciting interest as the core component of micro combined heat and power (CHP) units, in which it is more efficient and safer than a comparable steam engine.
Action of an alpha type Stirling engine
The following diagrams do not show internal heat exchangers in the compression and expansion spaces, which are needed to produce power. A regenerator would be placed in the pipe connecting the two cylinders. The crankshaft has also been omitted.
1. Most of the working gas is in contact with the hot cylinder walls, it has been heated and expansion has pushed the hot piston to the bottom of its travel in the cylinder. The expansion continues in the cold cylinder, which is 90° behind the hot piston in its cycle, extracting more work from the hot gas.
The Stirling engine is a heat engine that is vastly different from the internal-combustion engine in your car. Invented by Robert Stirling in 1816, the Stirling engine has the potential to be much more efficient than a gasoline or diesel engine. But today, Stirling engines are used only in some very specialized applications, like in submarines or auxiliary power generators for yachts, where quiet operation is important. Although there hasn't been a successful mass-market application for the Stirling engine, some very high-power inventors are working on it.
A Stirling engine uses the Stirling cycle, which is unlike the cycles used in internal-combustion engines.
The gasses used inside a Stirling engine never leave the engine. There are no exhaust valves that vent high-pressure gasses, as in a gasoline or diesel engine, and there are no explosions taking place. Because of this, Stirling engines are very quiet.
The Stirling cycle uses an external heat source, which could be anything from gasoline to solar energy to the heat produced by decaying plants. No combustion takes place inside the cylinders of the engine.
Popular Posts
-
Stirling Energy Systems' 25 kW solar dish harnesses the power of the sun to make zero emissions energy. Stirling Energy Systems (SES) is...
-
A Gamma type Stirling engine uses a displacer like a Beta Stirling but the power piston is mounted in a separate cylinder alongside the disp...
-
A Beta type Stirling engine has a single power piston and a displacer within the same cylinder and on the same shaft. The displacer piston i...
-
An Alpha type Stirling engine contains two power pistons in separate cylinders. One cylinder is hot and one cold. The hot piston is situated...
-
A Stirling engine is a heat engine operating by cyclic compression and expansion of air or other gas, the working fluid, at different temper...
-
25th October 1790 – 6th June 1878 was a Scottish clergyman, and inventor of the Stirling engine. Born at Cloag Farm near Methven, Perthsh...
-
The Stirling engine is a heat engine that is vastly different from the internal-combustion engine in your car. Invented by Robert Stirling i...
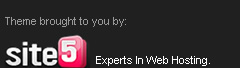